The Duravant family of operating companies serve the food processing, packaging and material handling segments.
Safety 101, Care Tips, & Training Resources
February 2022
A safe workplace not only protects employees from injury, it can also reduce absenteeism and turnover, lower injury or illness costs, increase productivity and quality, and raise employee morale.
In this edition of Service Advisor we will review general safety procedures when operating your processing equipment, cover cleaning tips for belts and other non-metallic parts, and highlight training resources for Key Technology sorters and shakers.
Safety 101
In this edition of Service Advisor we will review general safety procedures when operating your processing equipment, cover cleaning tips for belts and other non-metallic parts, and highlight training resources for Key Technology sorters and shakers. When thinking about workplace safety and addressing hazards the focus is often on addressing the larger risks, and rightfully so. While these hazards need to be taken seriously, and properly mitigated, it is important not to overlook the “little things”. When it comes to workplace safety, the little things are often the big things. Below are general safety guidelines that should be followed by anyone operating on, or near, your Key Technology equipment.
- Ensure that all safety guards and shields are securely fastened in place before starting your equipment.
- Read the entire manual before attempting to install, operate, or performing maintenance.
- Only authorized, properly trained personnel should be permitted to operate, install or maintain the equipment.
- Before removing any safety guards or covers, turn the system off and lock out the power.
- Keep the work area clean to prevent accidents and product contamination.
- Use your Key equipment only for tasks for which it was designed.
- Follow all specifications for space clearance, utilities, and environment which are provided on the equipment system assembly drawings.
- Keep the equipment in good working order at all times by performing regularly scheduled maintenance and conducting periodic safety inspections.
- Correct all unsafe conditions immediately.
- Do not wear torn or loose clothing or jewelry around any equipment with moving parts and always wear approved eye and ear protection.
- Do not walk or stand on the equipment; it is not safe as a walkway, platform, or ladder. Injuries or damage to the equipment or parts may occur.
- The combination of water and product can cause floors to become slippery and hazardous. To avoid injury form slipping and falling, exercise extreme care while working near the equipment.
Care Tips for Belts and other Non-Metallic Conveyor Components
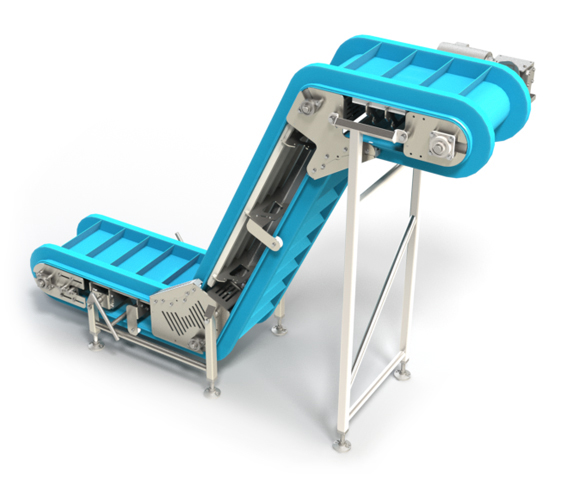
- belts made of polyester, polyurethane, or PVC;
- infeed and discharge rollers lagged with polyurethane
Most of the chemicals used for equipment cleaning and sanitizing also degrade the properties of polymers and may reduce the useful life of the belts and roller lagging. The effect on polyurethane of any chemicals containing chlorine is particularly severe.
Keeping the equipment in a proper sanitary condition is always the first priority in a food plant. Below are some measures that can be taken to maximize conveyor belt and roller lagging life:
- Advise your sanitation chemical supplier about the presence of the above polymers when getting material, mixing, and asking for application recommendations, as appropriate.
- Before applying chemicals, remove as much of the soil as possible with clear water. Use water at the temperature specified by your sanitation and plant safety departments, but not exceeding 140°F (60°C).
- Ensure that sanitation chemicals are not mixed to concentrations higher than what the chemical supplier and your sanitation department require.
- Do not leave cleaning and sanitizing chemicals on belts and rollers longer than the required time. Rinse thoroughly with clear water at the end of that time.
- Do not allow strong acids such as hydrochloric, nitric, or sulfuric to come in contact with belts or roller lagging.
- Do not apply solvents such as benzene, gasoline, MEK, trichloroethyene, or turpentine to belts or roller lagging. Use a soap solution and a soft scrub brush to remove any greasy stains.
Prevent Unplanned Downtime
Proactive maintenance is crucial to ensuring you’re getting the most out of your equipment and keeping your plant running efficiently. To prevent unplanned downtime and be certain your equipment is in optimal condition, we recommend an annual Equipment Audit.
An annual Equipment Audit can provide you with opportunities to reduce the number of urgent and emergency interruptions to operations because of equipment failure, as well as the total costs associated with maintenance. Our SupportPro service technicians can help customize an audit tailored to your specific equipment, and can assist in identifying, and providing, any required parts.
Training
Qualified people are getting harder and harder to recruit. when you do find the right person, make sure they have the training needed to operate the equipment.
Optimal operation is the result of people understanding what the equipment is supposed to be doing, knowing what your product quality requirements are, and understanding how to achieve that by managing the systems.
Schedule onsite training with one of our trainers or inquire about our online training today to ensure all of your operators are knowledgeable and ready for the upcoming season.
We Are Here to Help!
Our global SupportPro service team is here to assist you with all of your training, service and parts needs. Contact us today – we’re always here to help you meet your processing goals!